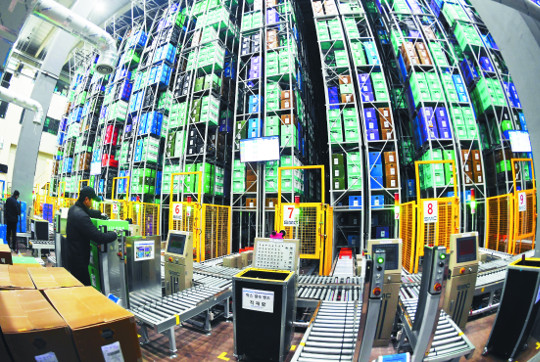
파란색과 초록색, 보라색 등 형형색색의 상자들이 레일 위를 타고 흐른다. 바코드 스캐너에서 ‘삑’ 하는 소리와 함께 목적지를 지정하면 노란색 크레인이 최대 60m 높이까지 쉴 새 없이 상자를 실어 나른다.
지난 1월 30일 찾은 인천 서구의 화장품 용기 제조사 ‘연우’의 물류센터. 1983㎡(600평) 규모의 물류센터에 사람이라고는 화장품 용기를 만드는 데 필요한 부품 상자를 레일 위에 올리는 협력사 직원 3~4명뿐이었다. 이동수 연우 경영정보팀장은 “자동 창고관리시스템(WMS) 도입 후 물류 이동·관리 등에 필요한 인력 60%를 생산 또는 품질 관련 부서로 옮겼기 때문”이라고 설명했다.
㈜연우는 2014년 말부터 스마트공장 구축에 속도를 내고 있다. 스마트공장은 재고관리, 생산, 물류, 판매 등 공장 운영 전반에 정보통신기술(ICT)을 접목한 것이다. 스마트공장 일종인 WMS도 지난해 3월 80억원을 들여 완성했다. LG생활건강과 아모레퍼시픽, 로레알, 에스티로더 등 세계 100대 화장품 기업 50%가 연우의 고객사다. 잘나가는 기업이 스마트공장 구축에 사활을 건 까닭을 묻자 이 팀장은 “과거 방식으로는 더 이상 효율적으로 회사를 운영하기 어렵다고 판단했기 때문”이라고 답했다.
우선 화장품 용기 자재 생산공정 중 첫 과정인 사출라인부터 손봤다. 협력사가 실시간으로 발주 현황을 확인할 수 있게 해 자재 생산속도를 한층 끌어올렸다. 이 팀장은 “얼마 전만 해도 구매팀이 전화나 팩스로 협력사에 일일이 발주했는데 이 작업에만 1~2일이 걸렸다”며 “이제는 몇 분이면 된다”고 말했다.
금속 화학연마라인에는 6억원을 들여 로봇을 도입했다. 그 결과 직원들이 황산 등 유해화학물질에 노출될 가능성을 최소화하고 불량률도 과거 2.7%에서 0.12%로 떨어졌다. 이밖에 회사 정보를 통합·관리하는 디지털 생산관리시스템(MES)을 구축해 생산계획, 실적관리, 품질관리, 금형과 설비관리 등을 시작했다. 기업자원관리 프로그램(ERP)도 도입해 현장 업무프로세스에 대한 지식을 암묵지(학습과 경험으로 체화돼 겉으로는 드러나지 않는 노하우)에서 형식지(문서나 매뉴얼처럼 외부로 표출돼 여러 사람이 공유하는 지식)로 전환시켜 직원 간 소통을 강화했다.
스마트공장 도입 효과는 컸다. 공장가동률이 이전과 비교해 평균 10% 포인트 뛰었다. 효율성이 좋아지니 매출도 2014년 약 1688억원에서 지난해 2729억원으로 늘었다. 같은 기간 직원 수는 1271명에서 1572명으로 증가했다. 스마트공장이 일자리를 빼앗을 것이라는 편견을 깨는 수치다.
스마트공장 도입에는 정부와 삼성전자 등 대기업의 전폭적인 협조가 있었다. 연우의 스마트공장 도입은 현재 진행형이다. 연우는 추가로 7억3000만원을 들여 오는 5월 도입 목표로 제품수명주기관리(PLM)와 생산계획지동화시스템(APS)을 구축할 계획이다.
인천=손재호 기자 sayho@kmib.co.kr