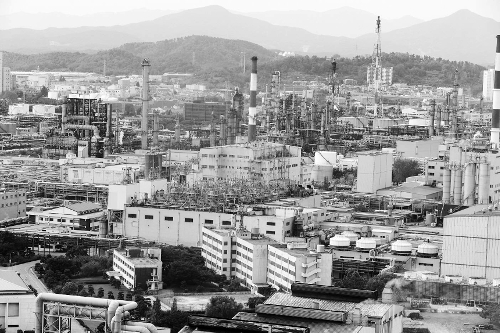
지난 4일 울산광역시 남구 매암동에 위치한 세계 1위 타이어코드 기업 효성의 울산 공장을 찾았다. 공장에 들어선 순간 쉴 새 없이 돌아가는 연사기(실에 꼬임을 주는 기계) 소리로 가득했다. 타이어코드는 타이어 형태를 잡아주고, 외부 힘에 변형되지 않도록 버티는 역할을 하는 핵심 소재다. 효성 제품은 2000년대 이후 글로벌 타이어코드 시장에서 1위 자리를 지키고 있다.
효성 울산공장은 ▲원유에서 만든 폴리에스테르(PET)를 실로 뽑아내는 방사 ▲실을 꼬아내는 연사 ▲연사를 천으로 짜내는 제직 ▲제품을 완성하는 열처리 단계를 통해 타이어코드를 생산하는 일관 생산체계를 갖췄다. 현장에서 만난 김호용 울산공장 기술혁신팀 과장의 도움으로 울산 타이어코드 공장의 전체 공정을 둘러볼 수 있었다.
가장 먼저 대형 원료 탱크와 아파트 10층 높이의 중합탑(원료 합성설비)이 눈에 늘어왔다. 중합 탑에서 타이어코드 원료인 PET 칩은 열과 압력을 통해 중합해 점도를 높인 후 공정의 첫 단계인 방사에 사용된다.
김 과장의 안내에 따라 핵심 라인인 방사 설비장으로 들어섰다. 섬유 생산공정 특성상 24시간 가동되는 탓에 윙윙거리는 소리가 귀를 때렸다. 옆 사람의 말이 들리지 않을 정도다. 다만 대부분 공정이 자동화된 덕택에 소음에 노출된 노동자는 거의 없었다. 거대한 방사기는 PET칩 을 녹여 노즐을 통해 원사를 국수처럼 뽑아내고 있었다. 노즐을 통해 실이 나오는 방사 속도는 1분당 5000m에 달한다는 김 과장의 설명이 이어졌다. 다음 공정인 연사와 제직도 눈여겨 볼만했다. 연사 과정은 얇은 원사를 2~3가닥으로 꼬아서 강력하고 튼튼한 연사로 제작하는 단계다. 생산된 연사는 하얀 빛을 띄고 있었다. 이런 연사 1500개 정도가 모여 하나의 천이 되는 것이 제직이다. 제직 과정 이후 천 형태의 원단에 2가지 종류의 화학 접착액을 발라 열처리를 하면 타이어코드로 완성된다. 이 과정에서 흰 빛을 띄던 타이어코드는 잘 익은 밤색으로 변했다.
제작된 타이어코드는 미셰린과 브리지스톤, 굿이어 등 세계 100곳 이상의 글로벌 타이어사에 납품된다. 전 세계 자동차 2대 중 1대의 타이어에는 효성 제품이 들어간다고 한다. 명실상부한 세계 1위 제품인 셈이다.
생산과정 전체가 자동화 공정을 통해 수준 높은 안정성을 확보했다는 점과 현장에서 만난 공장 노동자들에게서 세계 최고 품질을 향한 의지가 느껴졌다. 글로벌 시장에서 18년째 사랑받는 제품의 비결이 무엇이냐는 물음에 현장 관계자들에게서 “몸에 지닌 작은 기술이 천만금의 재산보다 낫다”는 답이 돌아왔다. 공장 관계자들은 “창업주인 조홍제 선대 회장의 말”이라며 “최고의 기술을 향한 노력이 현재의 결과를 만들었다. 완벽한 품질이 어떤 가치보다 중요하다”고 강조했다.
이어 “아프리카를 제외한 중국·베트남·미국·룩셈부르크 등 세계 주력 거점 시장에 생산기지를 보유한 것도 강점”이라며 “글로벌 생산 네트워크 구축을 통해 세계 각 지역에 있는 글로벌 고객들의 요구에 적시에 대응하고, 최적화된 맞춤형 서비스가 가능했다”고 강조했다. 올해 목표에 대해서는 “최근 중국 경쟁사들의 저가 공세가 계속되고 있다”며 “울산공장은 차별화된 ‘안전 제품’ 생산을 통해 고객 만족도를 더욱 높일 것”이라고 힘줘 말했다.
쿠키뉴스 기자 im9181@kukinews.com